



Therm
Therm
Therm
Extract actionable insights from your drone data and collaborate in real time using SenseHawk Therm, an integrated, cloud-based desktop & mobile solution. Accessible, anytime, and anywhere.
Extract actionable insights from your drone data and collaborate in real time using SenseHawk Therm, an integrated, cloud-based desktop & mobile solution. Accessible, anytime, and anywhere.
Extract actionable insights from your drone data and collaborate in real time using SenseHawk Therm, an integrated, cloud-based desktop & mobile solution. Accessible, anytime, and anywhere.



High-precision, IEC-compliant thermography scans for solar
High-precision, IEC-compliant thermography scans for solar
Conduct high-resolution thermal scans that are compliant with IEC standards. Achieve rapid turnaround times powered by AI-driven detections with 99% accuracy on a scalable, cloud-based platform.
Conduct high-resolution thermal scans that are compliant with IEC standards. Achieve rapid turnaround times powered by AI-driven detections with 99% accuracy on a scalable, cloud-based platform.
Conduct high-resolution thermal scans that are compliant with IEC standards. Achieve rapid turnaround times powered by AI-driven detections with 99% accuracy on a scalable, cloud-based platform.
High-precision, IEC-compliant thermography scans for solar
View and filter defects on a site map
View and filter defects on a site map
Integrate aerial IR scan data to digitally map defects on a aerial thermographic view of the site. Get a comprehensive list of defects that can be converted into tasks. View and filter defects by type.
Integrate aerial IR scan data to digitally map defects on a aerial thermographic view of the site. Get a comprehensive list of defects that can be converted into tasks. View and filter defects by type.
Integrate aerial IR scan data to digitally map defects on a aerial thermographic view of the site. Get a comprehensive list of defects that can be converted into tasks. View and filter defects by type.
View and filter defects on a site map
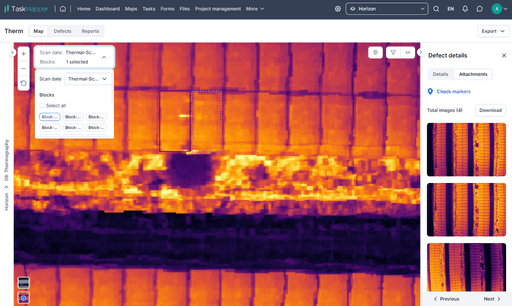
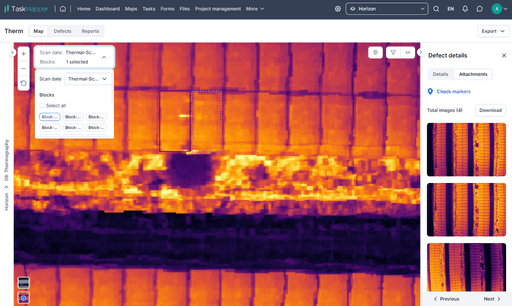
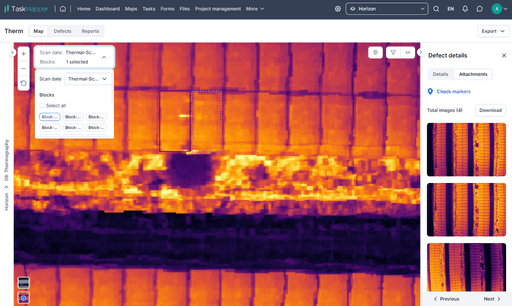



Create and monitor remediation tasks
Create and monitor remediation tasks
Select individual or bulk defects to create tasks and choose the required action. Create tasks and add assignees. Update status, priority, due date, category, and tags. Filter and export defect reports in PDF and CSV formats.
Select individual or bulk defects to create tasks and choose the required action. Create tasks and add assignees. Update status, priority, due date, category, and tags. Filter and export defect reports in PDF and CSV formats.
Select individual or bulk defects to create tasks and choose the required action. Create tasks and add assignees. Update status, priority, due date, category, and tags. Filter and export defect reports in PDF and CSV formats.
Create and monitor remediation tasks
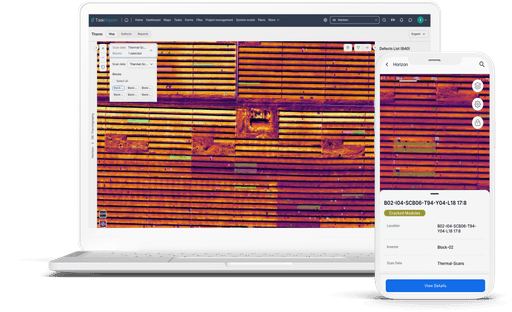
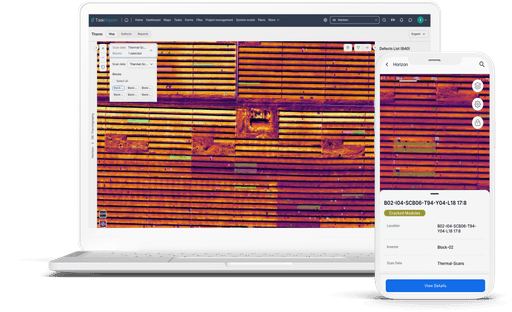
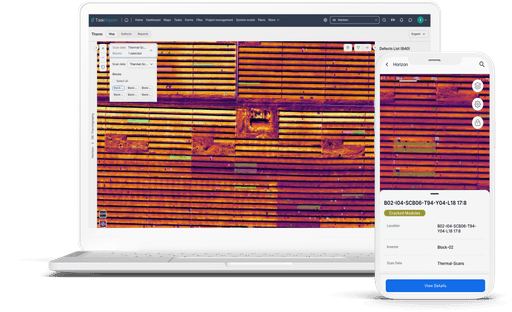
Accelerate operations with insights from aerial intelligence
Accelerate operations with insights from aerial intelligence
Accelerate operations with insights from aerial intelligence
Inspect, measure, analyse, and remediate defects on your site quickly.
Inspect, measure, analyse, and remediate defects on your site quickly.
Inspect, measure, analyse, and remediate defects on your site quickly.
Optimize inspections. Schedule scans to get detailed reports to support warranty claims, and defect locations to reduce and prevent downtime for all your assets.
Optimize inspections. Schedule scans to get detailed reports to support warranty claims, and defect locations to reduce and prevent downtime for all your assets.
Optimize inspections. Schedule scans to get detailed reports to support warranty claims, and defect locations to reduce and prevent downtime for all your assets.
Gain precise insights with prioritization to help monitor and manage your PV and thin film installs at different stages of the asset lifecycle.
Gain precise insights with prioritization to help monitor and manage your PV and thin film installs at different stages of the asset lifecycle.
Gain precise insights with prioritization to help monitor and manage your PV and thin film installs at different stages of the asset lifecycle.
Reduce costs and increase speed and accuracy of insights from aerial scans
Reduce costs and increase speed and accuracy of insights from aerial scans
Reduce costs and increase speed and accuracy of insights from aerial scans
Inspect, analyze and remediate defects on your site at a fraction of the cost and time taken for ground inspections. View, prioritize, assign and manage remediation tasks from your desk or in the field.
Inspect, analyze and remediate defects on your site at a fraction of the cost and time taken for ground inspections. View, prioritize, assign and manage remediation tasks from your desk or in the field.
Inspect, analyze and remediate defects on your site at a fraction of the cost and time taken for ground inspections. View, prioritize, assign and manage remediation tasks from your desk or in the field.
Accelerate time to remediation with tasks on a map
Accelerate time to remediation with tasks on a map
Help field executives plan better and work faster. Navigate to geolocated defects using the integrated mobile app. Keep collaboration in context using in-built chat with image and video attachments.
Help field executives plan better and work faster. Navigate to geolocated defects using the integrated mobile app. Keep collaboration in context using in-built chat with image and video attachments.
Help field executives plan better and work faster. Navigate to geolocated defects using the integrated mobile app. Keep collaboration in context using in-built chat with image and video attachments.
Accelerate time to remediation with tasks on a map






Improve collaboration between teams with chat and workflows
Improve collaboration between teams with chat and workflows
Integrate and track communications between teams to respond and manage work in real time. Simplify communications to get teams the help they need when they need it. Configure alerts, schedule notifications, and optimize your workflows for efficiency.
Integrate and track communications between teams to respond and manage work in real time. Simplify communications to get teams the help they need when they need it. Configure alerts, schedule notifications, and optimize your workflows for efficiency.
Integrate and track communications between teams to respond and manage work in real time. Simplify communications to get teams the help they need when they need it. Configure alerts, schedule notifications, and optimize your workflows for efficiency.
Improve collaboration between teams with chat and workflows
Enrich reports and updates from the field with visuals and notes
Enrich reports and updates from the field with visuals and notes
Capture your observations and defect details and updates on the mobile app during a site visit. Add images or videos, annotate, and share, to provide visual updates with geo-tagged issue locations for corrective action. Keep teams up to date on progress and status.
Capture your observations and defect details and updates on the mobile app during a site visit. Add images or videos, annotate, and share, to provide visual updates with geo-tagged issue locations for corrective action. Keep teams up to date on progress and status.
Capture your observations and defect details and updates on the mobile app during a site visit. Add images or videos, annotate, and share, to provide visual updates with geo-tagged issue locations for corrective action. Keep teams up to date on progress and status.
Enrich reports and updates from the field with visuals and notes






Monitor defect details on a dashboard for at-a-glance insights
Monitor defect details on a dashboard for at-a-glance insights
dashboard for at-a-glance insights Track defect occurrence over time to identify and address degradation of onsite components. Identify any recurring defects that could lead to potential points of failure. Optimize maintenance schedules to manage costs without hindering performance and yield.
dashboard for at-a-glance insights Track defect occurrence over time to identify and address degradation of onsite components. Identify any recurring defects that could lead to potential points of failure. Optimize maintenance schedules to manage costs without hindering performance and yield.
dashboard for at-a-glance insights Track defect occurrence over time to identify and address degradation of onsite components. Identify any recurring defects that could lead to potential points of failure. Optimize maintenance schedules to manage costs without hindering performance and yield.
Monitor defect details on a dashboard for at-a-glance insights
Simplify warranty claims with access to details of defects
Simplify warranty claims with access to details of defects
Identify defects caused by manufacturing or material quality. Use the SenseHawk Scan App to scan barcode data to geo-tag onsite components and store serial numbers. Use the map-based SenseHawk app to locate defective components onsite. Attach relevant component details, and add to Tasks along with the relevant workflow template to simplify your warranty claims.
Identify defects caused by manufacturing or material quality. Use the SenseHawk Scan App to scan barcode data to geo-tag onsite components and store serial numbers. Use the map-based SenseHawk app to locate defective components onsite. Attach relevant component details, and add to Tasks along with the relevant workflow template to simplify your warranty claims.
Identify defects caused by manufacturing or material quality. Use the SenseHawk Scan App to scan barcode data to geo-tag onsite components and store serial numbers. Use the map-based SenseHawk app to locate defective components onsite. Attach relevant component details, and add to Tasks along with the relevant workflow template to simplify your warranty claims.
Simplify warranty claims with access to details of defects



After upgrading to TaskMapper, I have cut the 20-25 hours (of work) down to about 2. Not to mention the massive increase in quality of the SenseHawk report versus the typical Excel or Bluebeam-generated reports by superintendents.
Zachary Matheny, Project Administrator, Blue Ridge Power
SenseHawk is one of the leaders in leveraging new age technologies for improved solar asset management, and we have been successfully working with them for the last 2 years with good results
Sunil Modi, Head O&M, Adani Group
Having collaborated with SenseHawk for the past 3+ years, we have consistently experienced a level of reliability and competence that has contributed positively to the success of our projects.
Varun Singhal, Head – O&M, Performance, Sterling and Wilson Renewable Energy Limited
After upgrading to TaskMapper, I have cut the 20-25 hours (of work) down to about 2. Not to mention the massive increase in quality of the SenseHawk report versus the typical Excel or Bluebeam-generated reports by superintendents.
Zachary Matheny, Project Administrator, Blue Ridge Power
SenseHawk is one of the leaders in leveraging new age technologies for improved solar asset management, and we have been successfully working with them for the last 2 years with good results
Sunil Modi, Head O&M, Adani Group
Having collaborated with SenseHawk for the past 3+ years, we have consistently experienced a level of reliability and competence that has contributed positively to the success of our projects.
Varun Singhal, Head – O&M, Performance, Sterling and Wilson Renewable Energy Limited
After upgrading to TaskMapper, I have cut the 20-25 hours (of work) down to about 2. Not to mention the massive increase in quality of the SenseHawk report versus the typical Excel or Bluebeam-generated reports by superintendents.
Zachary Matheny, Project Administrator, Blue Ridge Power
SenseHawk is one of the leaders in leveraging new age technologies for improved solar asset management, and we have been successfully working with them for the last 2 years with good results
Sunil Modi, Head O&M, Adani Group
Having collaborated with SenseHawk for the past 3+ years, we have consistently experienced a level of reliability and competence that has contributed positively to the success of our projects.
Varun Singhal, Head – O&M, Performance, Sterling and Wilson Renewable Energy Limited
After upgrading to TaskMapper, I have cut the 20-25 hours (of work) down to about 2. Not to mention the massive increase in quality of the SenseHawk report versus the typical Excel or Bluebeam-generated reports by superintendents.
Zachary Matheny, Project Administrator, Blue Ridge Power
SenseHawk is one of the leaders in leveraging new age technologies for improved solar asset management, and we have been successfully working with them for the last 2 years with good results
Sunil Modi, Head O&M, Adani Group
Having collaborated with SenseHawk for the past 3+ years, we have consistently experienced a level of reliability and competence that has contributed positively to the success of our projects.
Varun Singhal, Head – O&M, Performance, Sterling and Wilson Renewable Energy Limited
After upgrading to TaskMapper, I have cut the 20-25 hours (of work) down to about 2. Not to mention the massive increase in quality of the SenseHawk report versus the typical Excel or Bluebeam-generated reports by superintendents.
Zachary Matheny, Project Administrator, Blue Ridge Power
SenseHawk is one of the leaders in leveraging new age technologies for improved solar asset management, and we have been successfully working with them for the last 2 years with good results
Sunil Modi, Head O&M, Adani Group
Having collaborated with SenseHawk for the past 3+ years, we have consistently experienced a level of reliability and competence that has contributed positively to the success of our projects.
Varun Singhal, Head – O&M, Performance, Sterling and Wilson Renewable Energy Limited
After upgrading to TaskMapper, I have cut the 20-25 hours (of work) down to about 2. Not to mention the massive increase in quality of the SenseHawk report versus the typical Excel or Bluebeam-generated reports by superintendents.
Zachary Matheny, Project Administrator, Blue Ridge Power
SenseHawk is one of the leaders in leveraging new age technologies for improved solar asset management, and we have been successfully working with them for the last 2 years with good results
Sunil Modi, Head O&M, Adani Group
Having collaborated with SenseHawk for the past 3+ years, we have consistently experienced a level of reliability and competence that has contributed positively to the success of our projects.
Varun Singhal, Head – O&M, Performance, Sterling and Wilson Renewable Energy Limited
After upgrading to TaskMapper, I have cut the 20-25 hours (of work) down to about 2. Not to mention the massive increase in quality of the SenseHawk report versus the typical Excel or Bluebeam-generated reports by superintendents.
Zachary Matheny, Project Administrator, Blue Ridge Power
SenseHawk is one of the leaders in leveraging new age technologies for improved solar asset management, and we have been successfully working with them for the last 2 years with good results
Sunil Modi, Head O&M, Adani Group
Having collaborated with SenseHawk for the past 3+ years, we have consistently experienced a level of reliability and competence that has contributed positively to the success of our projects.
Varun Singhal, Head – O&M, Performance, Sterling and Wilson Renewable Energy Limited
After upgrading to TaskMapper, I have cut the 20-25 hours (of work) down to about 2. Not to mention the massive increase in quality of the SenseHawk report versus the typical Excel or Bluebeam-generated reports by superintendents.
Zachary Matheny, Project Administrator, Blue Ridge Power
SenseHawk is one of the leaders in leveraging new age technologies for improved solar asset management, and we have been successfully working with them for the last 2 years with good results
Sunil Modi, Head O&M, Adani Group
Having collaborated with SenseHawk for the past 3+ years, we have consistently experienced a level of reliability and competence that has contributed positively to the success of our projects.
Varun Singhal, Head – O&M, Performance, Sterling and Wilson Renewable Energy Limited
After upgrading to TaskMapper, I have cut the 20-25 hours (of work) down to about 2. Not to mention the massive increase in quality of the SenseHawk report versus the typical Excel or Bluebeam-generated reports by superintendents.
Zachary Matheny, Project Administrator, Blue Ridge Power
SenseHawk is one of the leaders in leveraging new age technologies for improved solar asset management, and we have been successfully working with them for the last 2 years with good results
Sunil Modi, Head O&M, Adani Group
Having collaborated with SenseHawk for the past 3+ years, we have consistently experienced a level of reliability and competence that has contributed positively to the success of our projects.
Varun Singhal, Head – O&M, Performance, Sterling and Wilson Renewable Energy Limited
After upgrading to TaskMapper, I have cut the 20-25 hours (of work) down to about 2. Not to mention the massive increase in quality of the SenseHawk report versus the typical Excel or Bluebeam-generated reports by superintendents.
Zachary Matheny, Project Administrator, Blue Ridge Power
SenseHawk is one of the leaders in leveraging new age technologies for improved solar asset management, and we have been successfully working with them for the last 2 years with good results
Sunil Modi, Head O&M, Adani Group
Having collaborated with SenseHawk for the past 3+ years, we have consistently experienced a level of reliability and competence that has contributed positively to the success of our projects.
Varun Singhal, Head – O&M, Performance, Sterling and Wilson Renewable Energy Limited
After upgrading to TaskMapper, I have cut the 20-25 hours (of work) down to about 2. Not to mention the massive increase in quality of the SenseHawk report versus the typical Excel or Bluebeam-generated reports by superintendents.
Zachary Matheny, Project Administrator, Blue Ridge Power
SenseHawk is one of the leaders in leveraging new age technologies for improved solar asset management, and we have been successfully working with them for the last 2 years with good results
Sunil Modi, Head O&M, Adani Group
Having collaborated with SenseHawk for the past 3+ years, we have consistently experienced a level of reliability and competence that has contributed positively to the success of our projects.
Varun Singhal, Head – O&M, Performance, Sterling and Wilson Renewable Energy Limited
After upgrading to TaskMapper, I have cut the 20-25 hours (of work) down to about 2. Not to mention the massive increase in quality of the SenseHawk report versus the typical Excel or Bluebeam-generated reports by superintendents.
Zachary Matheny, Project Administrator, Blue Ridge Power
SenseHawk is one of the leaders in leveraging new age technologies for improved solar asset management, and we have been successfully working with them for the last 2 years with good results
Sunil Modi, Head O&M, Adani Group
Having collaborated with SenseHawk for the past 3+ years, we have consistently experienced a level of reliability and competence that has contributed positively to the success of our projects.
Varun Singhal, Head – O&M, Performance, Sterling and Wilson Renewable Energy Limited
Customers in
Countries
Satisfied Customers
Solar Sites & Assets
GW
Supported
ISO
27001
Certified
Countries
Customers in
Satisfied Customers
Solar Sites & Assets
GW
Supported
ISO
27001
Certified
Countries
Customers in
Satisfied Customers
Solar Sites & Assets
GW
Supported
Certified
27001
ISO
TaskMapper Solar
Products
TaskMapper Solar
Products
TaskMapper Solar