A leading utility-scale solar operator in the US uses TaskMapper to digitize and transform the management of its assets and enhance operational efficiency.
At a Glance
A utility-scale solar energy operator wants to digitize its solar assets in the United States to enhance operational efficiency. Manual creation of solar panel records and verification of design versus as-built will be time-consuming and prone to error.
SenseHawk proposes using its TaskMapper platform for solar and the integrated mobile apps to streamline operations. Using the barcode scanning tool, SCAN, component data across the sites is digitally captured and mapped onto digital models of the power plants on the platform.
Operations crews can now use the fieldworker friendly, map-based mobile app, to easily navigate sites, achieve quicker event response times, and increase O&M efficiency.
The Need
A prominent owner, developer, and operator of utility-scale solar wants to digitize 4 GW of solar site operations in the United States. Manually creating records of solar panels by location and verifying that module installations are as per design will be time-consuming and error-prone.
The operator has historically tracked barcodes only at the lot level, i.e., which batch of modules is installed and linked to which inverter. In the event of manufacturing defects, or product recalls for specific lots, field teams will have to examine up to 10,000 modules per inverter block to identify specific modules for replacement or repair.
Since solar photovoltaic (PV) powerplants typically have up to 3 million panels installed for each GW of capacity, the ability to identify and access the right panels in a timely manner is critical for operations and maintenance. Access to this information can assist construction teams in better managing commissioning punch lists and O&M teams in lowering operational costs.
The Solution
SenseHawk proposes using the SCAN mobile app for inventory mapping. Integrated with TaskMapper, it helps automate the process of component serial number capture onsite. The serial numbers are geo-referenced to the digital twin of the component on the digital site model created on the platform. The digitized data is now accessible over the TaskMapper web and mobile interfaces for real-time coordination at jobsites and contextual communication.
Geo-referencing individual modules and their exact position within a tracker to the digital twin of the site on TaskMapper makes it easy to verify that module installations are as per design. The digital model contains other details of each component, including OEM and watt-peak capacity.
Office teams can now create tasks associated with any digital component. Onsite crews can view assigned tasks on their mobile devices and use map-based interface to navigate directly to the task location. They can access additional information and documents, collaborate using text, voice, or video, get expert help if required, update defect and remediation status, and add observations to the task and documents.
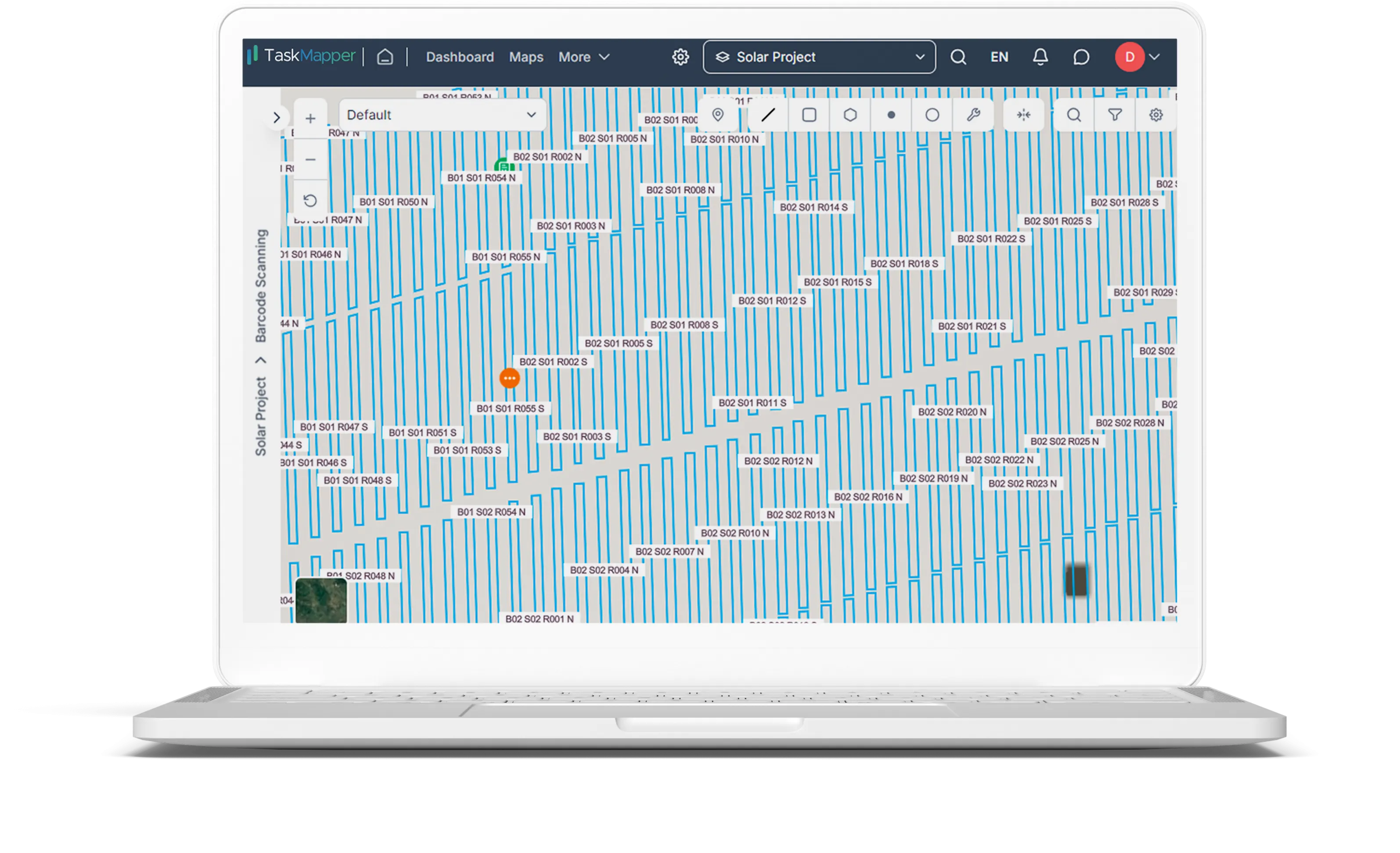
Real-time coordination using map-based desktop & mobile apps to enable timely access to information and updates
The Result
The solar operator wants to digitize its current 4 GW of solar operations in the US to pave the way for further expansion. With all asset data digitized using TaskMapper, the operator easily streamlines management processes and tracking. The digital twin of the site on the platform, built with system models that use location as the context, incorporates all physical site data with associated logical and hierarchical connections and interdependencies. The data mapped to the digital components can be further enriched with tasks, forms, checklists, sub tasks, and more.
Without having to search or enter lengthy discussions, field crews can use the mobile app and contextual chat under each task to directly navigate to task locations, access available data and resources, and tap into the collective knowledge of the teams to tackle the job at hand.
With all component data digitized, updating replacement component data and tracking inventory and warranty information become simpler. The fieldworker app, eases office-site communication and collaboration to increase O&M efficiency, and save time, manpower, and cost.

Manage site work easily with digitized tasks that incorporate location data, related files, pre-defined checklists, templetized forms, and provide a contextual chat option
Posted by
Related Tags
Solar PV, Digitization, Asset Management, Solar O&M, Field Teams, Mobile App, Digital Twins, Construction Monitoring, Quality Control, Workflows